Методы регулирования
усадки при литье термопластов под
давлением
Брагинский В.А., Барвинский И.А.,
Барвинская И.Е.
V Российский конгресс
переработчиков пластмасс. 14-15 ноября.
Москва. 2011. Препринт
Для получения
деталей из термопластов литьем под
давлением литьевая форма должна быть
изготовлена с учетом технологической
усадки (далее - усадки) полимерного
материала [1], однако
прогнозирование усадки для конкретной
детали связано с рядом проблем [2] из-за
сложности и неоднородности усадочных
процессов. Практически важна
возможность регулирования усадки в
ходе испытаний изготовленной формы без
механической доработки формы или с
минимальной доработкой по результатам
испытаний.
Целью данной работы
является разработка методологии
регулирования усадки по результатам
испытаний литьевой формы на основе
моделирования процесса литья
термопластов.
Усадочные процессы при
литье термопластов происходят
вследствие уменьшения объема (объемной
усадки) при охлаждении полимерного
материала от температуры расплава до
комнатной температуры при частичной
компенсации объемных изменений за счет
увеличения массы и плотности
полимерного материала в полости формы
на стадии подпитки. Поэтому
регулирование объемной усадки
является одним из возможных подходов
для регулирования усадки отливаемой
детали.
Выраженная в процентах
объемная усадка Sv может быть
определена по формуле [3]:
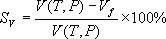
где V(T,
P) – средний удельный объем
расплава при температуре и давлении
расплава в полости после заполнения и
уплотнения, Vf
– средний удельный объем полимерного
материала при комнатной температуре и
атмосферном давлении. Объемную усадку
рассчитывают на основе PVT-данных термопласта при
известном давлении и температуре
расплава в полости формы. Оценка
объемной усадки может быть выполнена
графически с использованием PVT-диаграммы [4].
Распределение объемной усадки в
отливке можно получить при
моделировании стадий заполнения,
уплотнения и охлаждения отливки
численными методами.
Другим возможным
подходом при регулировании усадки
является регулирование анизотропии
усадки, обусловленной разницей
продольной и поперечной усадки, однако
данный подход трудно использовать на
практике. Во-первых, зависимость
анизотропии от конструктивных и
технологических факторов в
большинстве случаев имеет сложный
характер (см., например [5-6]) даже при
сравнительно простой конструкции
литьевой детали. Во-вторых, существует
проблема неопределенности понятий «продольной»
и «поперечной» усадок (и
соответственно анизотропии усадки) в
реальных деталях. Данная проблема
связана со сложным характером
деформирования расплава на стадиях
заполнения и уплотнения, который, в
частности, является причиной
неравномерной двухосной молекулярной
ориентации полимера, и изменениями
направлений течения расплава в
процессе заполнения и уплотнения. Для
материалов, содержащих жесткие
волокнистые наполнители, анизотропия
усадки обусловлена, главным образом,
ориентацией наполнителя.
Третий подход при
регулировании усадки - регулирование
процесса вязкоупругой релаксации
напряжений в отливке в то время, пока
она находится в форме, например, при
изменении времени выдержки на
охлаждение. Такой подход является
эффективным при отсутствии или
минимальном уровне усадки в форме. В
реальных деталях для некоторых
размеров усадка в форме невозможна из-за
геометрических ограничений. Например,
усадка на отверстии возможна только
после извлечении знака, формующего это
отверстие. Для других размеров при
адекватном уплотнении отливки
отсутствие усадки в форме
обеспечивается хорошим сцеплением
отливки с формующей поверхностью из-за
высокой шероховатости формующей
поверхности (как минимум с одной из
сторон литьевой детали) и короблением в
форме (в пределах усадки по толщине
отливки) [7].
При регулировании усадки
необходимо учитывать влияние
корректирующих действий на все
характеристики напряженно-деформированного
состояния детали, к которым, кроме
усадки, относятся поверхностные
деформации (утяжины), коробление,
остаточные напряжения. Также должны
учитываться: возможное появление
других поверхностных дефектов,
изменение внутренней структуры (появление
внутренних усадочных полостей, макро-
или микропористости) и ухудшение
эксплуатационных характеристик детали.
Для практической
реализации этих подходов могут
применяться: регулирование
технологического режима, внесение
изменений в конструкцию формы и
литьевой детали, замена полимерного
материала детали и использование
специальных технологий литья.
Хотя методы
регулирования усадки при изменении
технологического режима являются
наиболее предпочтительными, поскольку
они обеспечивают минимальные затраты,
их применение связано с рядом
ограничений. Для учета взаимовлияния
технологических параметров необходимо
использовать методы математической
статистики и планирования
эксперимента.
Наибольшее влияние на
усадку в большинстве случаев оказывает
давление выдержки: обычно усадка
уменьшается при повышении давления
выдержки. К исключениям относятся,
например, композиции термопластов, с
жестким волокном (согласно [5], усадка в
направлении волокна практически не
зависит от давления), а также некоторые
виды термопластичных эластомеров, для
которых может наблюдаться обратная
зависимость: усадка повышается при
увеличении давления выдержки [8].
К распространенным
конструктивным методам регулирования
усадки относятся доработка впускных
литников и изменение мест впуска.
Доработка впускных литников
эффективна для материалов, не
содержащих жесткого волокна (стеклянного,
углеродного и др.): небольшое
увеличение толщины тонкого впускного
литника может значительно увеличить
время уплотнения (время до отключения
полости от материального цилиндра),
соответственно улучшить уплотнение
детали и уменьшить усадку. Влияние
изменения мест впуска на усадку может
быть очень сложным, особенно для
материалов, наполненных жестким
волокном: изменение мест впуска может
привести к резкому изменению усадки и
анизотропии усадки.
При регулировании усадки
путем замены полимерного материала
необходимо учитывать тип полимера (или
смеси полимеров), типы и содержание
наполнителей, а также типы и содержание
добавок (даже при малом содержании
последних). Например, значительные
изменения усадки кристаллизующихся
термопластичных материалов на основе
полиэтилена, полипропилена, полиамидов
6 и 66, ПБТ и др. могут наблюдаться при
добавлении окрашивающих веществ,
которые в этом случае играют роль
нуклеаторов [9].
Наиболее удобны для
регулирования усадки композиции с
дисперсными наполнителями: повышение
содержания наполнителя приводит к
уменьшению усадки и анизотропии усадки.
Применение нанодобавок
приводит к большему снижению усадки
композита при увеличении содержания
наполнителя по сравнению с обычными
дисперсными наполнителями, однако этот
эффект проявляется только при малых
концентрациях наполнителя. В работе [10]
для композиций полипропилена
значительное снижение усадки
наблюдалось при добавлении наноглины в
диапазоне 0 – 4%. В то же время усадка
наиболее распространенных композиций
полипропилена, содержащих 20-40%
дисперсного наполнителя, существенно
ниже усадки нанокомпозитов с 4%
наполнителя.
Для регулирования усадки
могут применяться специальные
технологии литья термопластов: литье
со вспениванием (с использованием
порофоров, MuCell
и др.), компрессионное формование (литье
с подпрессовкой), литье с газом, литье с
вариотермическим термостатированием («пульсирующим»
охлаждением). Данные технологии
позволяют уменьшить объемную усадку
отливки по сравнению с обычным литьем
под давлением. Они эффективны в тех
случаях, когда при обычном литье
невозможно обеспечить адекватное
уплотнение полимерной детали, например
при повышенной толщине стенки. Каждая
из этих технологий имеет свои
преимущества и недостатки, в частности,
одной из проблем литья со вспениванием
является «серебристость» на
поверхности отливок. Для использования
большинства специальных технологий
требуется дополнительное оборудование
и модернизация литьевой формы.
Предварительное
моделирование процесса литья
термопластов под давлением с
использованием численных методов
позволяет повысить эффективность
обсуждаемых подходов регулирования
усадки. Рассмотрим в качестве примера
программные продукты Autodesk
Moldflow,
в которых моделируются стадии
заполнения, уплотнения и охлаждения
отливки в форме, а также рассчитывается
усадка полимерного материала.
Наибольшую точность прогнозирования
усадки дает метод «скорректированных
остаточных напряжений» (CRIMS) (см., например, [2]). Хотя в
настоящее время точность расчета
абсолютных значений усадки по этому
методу для реальных изделий во многих
случаях является недостаточной, данный
метод обеспечивает приемлемую по
сравнению с заданными допусками
точность расчета относительных
изменений усадки при изменении
технологических и конструктивных
факторов.
В табл. 1 приведены
результаты оценки относительного
влияния на среднюю усадку
технологических параметров процесса
литья, полученные с использованием
анализа чувствительности по методу
Тагути – см., например, [11] - в Autodesk
Moldflow Insight 2012 для модели двухместной
отливки (рис. 1, a) из АБС-пластика марки HI-121 компании LG
Chemicals.
Расчет проводился в 2.5D-анализе
с применением технологии анализа Dual-Domain и метода «скорректированных
остаточных напряжений». Толщина
основной стенки детали составляет 3 мм.
Из представленных результатов следует,
что наибольшее влияние на усадку в
заданном диапазоне условий оказывает
давление выдержки. Зависимость средней
расчетной усадки от давления выдержки
показана на рис. 1, б (расчеты
выполнялись при температурах расплава
и формы, соответствующих средним
значениям рекомендуемого диапазона
переработки
полимерного материала).
Моделирование
процесса литья позволяет оценить
диапазон изменения технологических
параметров, эффективность изменений
конструкции и замены материала детали
при регулировании усадки. Точность
таких оценок зависит от используемых
моделей (сетки - геометрической модели
изделия, процесса литья, материала и т.д.),
а также «модели качества» [12].
|